PFX Series
PLASTICS INK
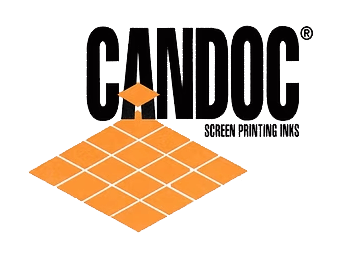
White*
Black*
Ultra Blue*
Medium Yellow*
Navy Blue*
Primrose Yellow* Medium Green*
Fire Red*
Orange*
Light Brown*
Maroon*
Flag Red*
Deep Red*
Perma Green*
Perma Blue*
Emerald Green*
Light Blue*
Lemon Yellow*
Dark Brown*
PFX-903
PFX-904
PFX-905
PFX-906
PFX-907
PFX-909
PFX-912
PFX-913
PFX-914
PFX-915
PFX-919
PFX-922
PFX-923
PFX-925
PFX-928
PFX-990
PFX-991
PFX-992
PFX-995
METALLIC COLORS
Pale Gold*
Rich Pale Gold*
Rich Gold*
Silver*
Bright Silver*
PFX-934
PFX-935
PFX-936
PFX-937
PFX-939
MIXING COLORS
Process Yellow LF*
Mixing Orange*
Rubine*
Rhodamine*
Purple*
Reflex Blue*
Cyan*
Green*
Mixing White*
Mixing Black*
Mixing Clear*
PFXMS-01
PFXMS-02
PFXMS-03
PFXMS-04
PFXMS-05
PFXMS-06
PFXMS-07
PFXMS-08
PFXMS-09
PFXMS-10
PFXMS-11
* Heavy metal compliant
STANDARD COLORS
Created primarily for screen printing Coroplast and similar polyethylene / polypropylene materials, PFX Series dries fast, offers good flexibility and outdoor durability; it is readily vacuum formable.
SUBSTRATES
Coroplast and similar fluted (corrugated) plastic sheets.
​Other plastics:
-
Acrylic*
-
Polycarbonate*
-
Vinyl fleet marking film*
-
Foamed vinyl such as Sintra*
-
Styrene*
​
​
​
​MODIFIERS
Thinner: PFX-901 to achieve desired viscosity
Retarder PFX-921 Retarder to slow in-screen drying
-
NOTE: Excessive use of retarder may inhibit drying of the printed film.
Flow Promoter: PFX-920 to improve ink flow out
Clear: PFX-902
Screen Wash: PFX-910
​
*PA SERIES Multi-Use Inks are recommended for
most types of plastic substrates.
SCREEN MESH
160 to 300+
Monofilament
STENCILS
Direct method
emulsions,
capillary films
SQUEEGEE
All types, 60 to 80 durometer
Fluorescent Colors
Blaze Orange* Aurora Pink*
Rocket Red*
Signal Green* Arc Yellow*
PFX-960
PFX-961
PFX-962
PFX-963
PFX-964
Fire Orange*
Neon Red*
Corona Magenta*
Horizon Blue* Saturn Yellow*
PFX-965
PFX-966
PFX-967
PFX-968
PFX-960
Because the shelf life of fluorescent inks cannot be guaranteed (particularly in warmer weather) fluorescent colors in the SS Series are offered in two part kits. Clear (Part B) are pre-modified for easier blending Pigments (Part A) are pre-measured. A small mixing unit is recommended.
​
Fluorescent color names are Trademarks of DayGlo Color Corporation.
FOR COROPLAST(TM), POLYETHYLENE
& POLYPROPYLENE

ALWAYS TEST INK WITH SUBSTRATE
PRIOR TO PRODUCTION!
Drying
PFX Series inks dry through solvent evaporation. Fresh air volume is more of a factor in dry time than temperature.
Force Dry:
For high volume air dryer (3000 - 5000 cfm, equipped with air knives) at 100 -120°F: 30 - 60 seconds.
Air Dry: 15 - 45 minutes depending on air circulation and temperature.​
Equipment: Batch oven with convection air or industrial conveyor dryer (non-textile) are preferred. lR panels may provide sufficient cure if belt will accommodate parameters above.
COVERAGE
Approximately 1200 Sq Ft / Gal.
Note: lnformation contained in Cudner & O’Connor product sheets is based on laboratory and field tests. Because we cannot control actual production conditions, no warranty is expressed or implied. Careful testing is always recommended prior to production. Consult with our Technical Services Department on all application issues.